Product development EXHAUST PLUG FOR VAILLANT
Thanks to flexible prototype development using 3D printing, we could deliver an ideal series product to our customer.
With the help of rapid prototyping, Würth Industrie Service developed a customised exhaust plug for Vaillant quickly and cost-effectively.
Initial situation: Solution needed for sealing exhaust pipe
For the safety of the service staff, Vaillant, which is internationally operational in the sector heating and climate technologies, has long been looking for a solution for reliable, gas-tight and acid-resistant sealing of exhaust pipes during the time window of maintenance and cleaning. Here, the challenge is that the pipe diameter of the standard exhaust pipe is bigger than the diameter of the maintenance openings.
Vaillant could not find or develop a product on its own, which can be inserted and removed during every maintenance and at the same time can seal the exhaust pipe completely and securely against flue gas, maintain temperatures from 10 °C to 90 °C and is acid-resistant. Besides, there should also be a visual signal from the outside when the component is inserted in the pipe, so that when the maintenance staff closes the lid, it is not forgotten inside the pipe.
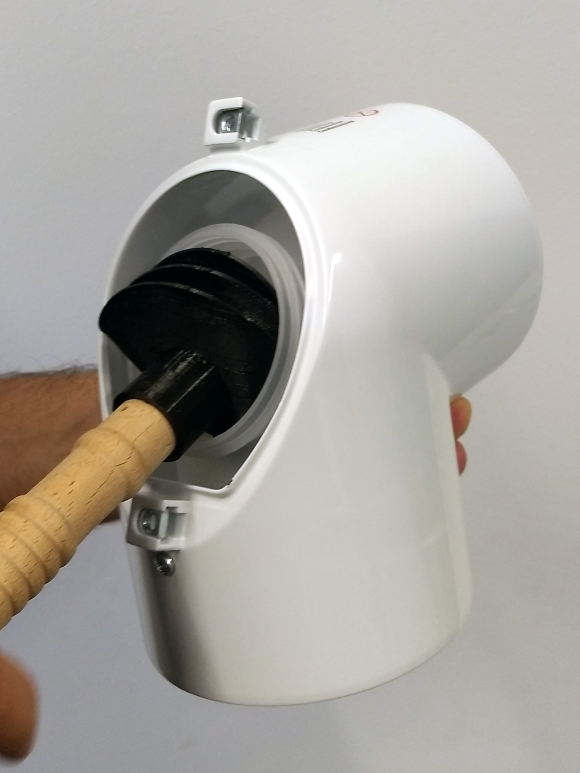
Würth Industrie Service undertakes design, development and prototype printing
As Würth Industrie Service has been working with Vaillant since a few years in international C-Parts Management, they approached Würth Industrie Service with the product requirement. The department "Design and Development" of Würth Industrie Service defined the technical and organisational framework for the product together with Vaillant and undertook the design and development.
Very soon after that, the first prototype was manufactured with the help of an in-house 3D printer with the elastic material TPU (Thermoplastic Polyurethan- Elastomere). This prototype was used for “look & feel” and for further optimisations. A waterproof printed pipe plug was mounted with four flexible slats on a printed handle. To gas-proof the pipe, the slats should be compressed during application and removal through the maintenance opening of the exhaust pipe. In the pipeline itself, they should again revert to the original state corresponding to the inner diameter. Additionally, an optical aid was installed upon the request of the customer to ensure that the component was not forgotten in the exhaust pipeline system at the end of the maintenance.
A second prototype followed which was already functional due the reduction in the wall thickness of the slats; however, it was still not made out of appropriate material needed for gas-proofing and acid-resistance. The additive handle was replaced by a wooden handle which was connected to the plug with a coupling mechanism and an adhesive surface, which in turn would prevent opposite torsion of both the components while inserting the plug in the pipeline system.
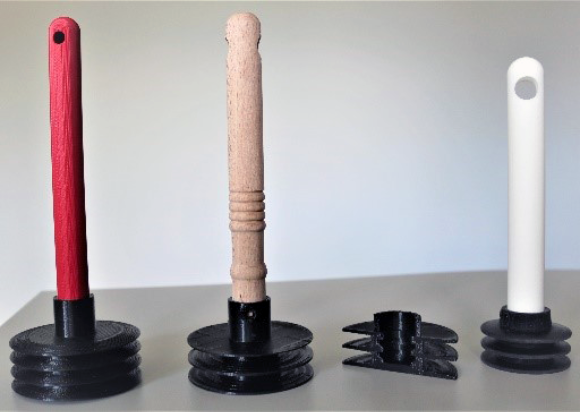
Final prototype development
With the use of suitable materials and a process changeover while 3D printing, the fourth product could be manufactured as the functional prototype and sent once again to Vaillant. Vaillant carried out leak tests and deemed the prototype as final.
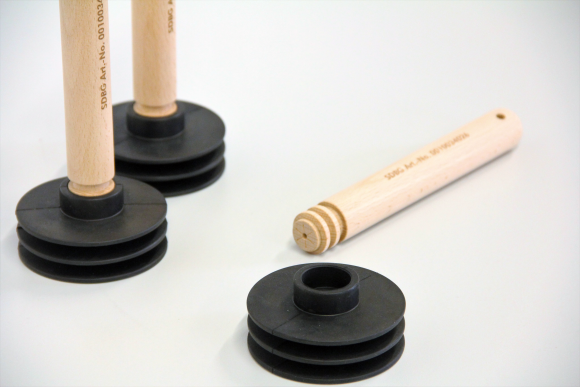
Series production in the injection moulding process
Because of the yearly purchase quantity, the injection moulding process has economic advantages over additive manufacturing in the production of exhaust plugs, which is why Würth Industrie Service suggested the process changeover to Vaillant and undertook the production in cooperation with a partner company.
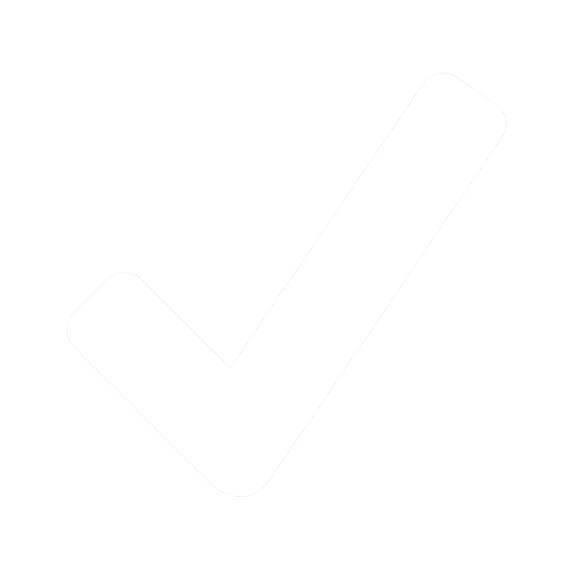
Factors of success:
With the use of additive manufacturing technology in the prototype development, a final prototype could be presented to Vaillant in a short time. Thanks to the experience with conventional manufacturing processes, it was possible for Würth Industrie Service to choose the best possible process for series production.
Würth Industrie Service supplies exhaust plugs to Vaillant as completely assembled, individually packaged, in the quantity required and at the desired delivery time.
Additional information
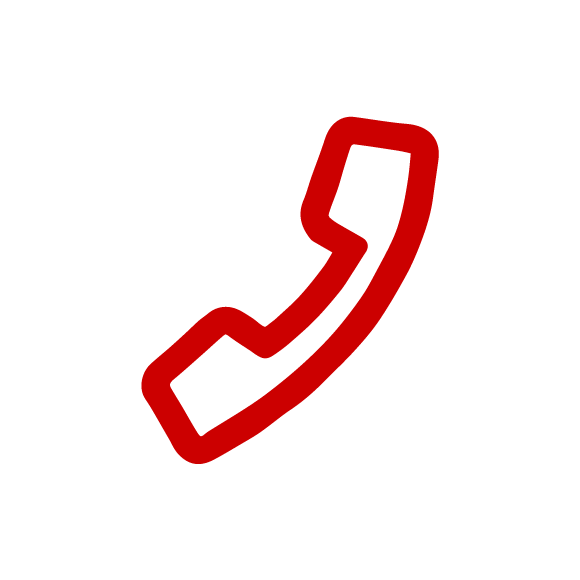
Contact
We are here for you!
Please contact us by telephone +49 7931 91 3972 or
via E-Mail under additivemanufacturing@wuerth-industrie.com.
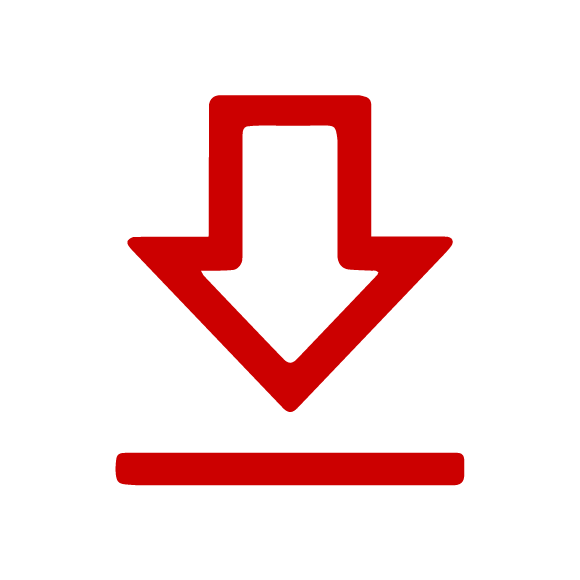
Websites can save or retrieve information in your browser in the form of Cookies. This may be anonymous statistical data, information about you, your settings or devices used, in order to enable a personalised web experience or so that the website works in the way you are expecting it to.
We respect your right to protection of your data. You can therefore decide not to accept certain types of Cookies. For an overview and the settings for the Cookies which we use, please see here. You can change these settings at any time, by invoking our Data protection declaration.
By saving, you confirm that you have understood the settings specified for Cookies and that you agree with them.
The Würth Industrie Service GmbH & Co. KG collects and processes the personal data provided in the form in order to process the requested request for you. Please note the mandatory fields in the forms. The legal basis for this processing, the absolutely necessary data, is Art. 6 para. 1 lit. b DSGVO, implementation of a pre-contractual measure. The processing of data voluntarily provided by you is carried out on the basis of Art. 6 para. 1 lit. f DSGVO. Thereafter, processing is permissible which is necessary to safeguard our legitimate interests. Our legitimate interest is to have contact with you, our customers, to improve our consulting quality and to be able to contact you more easily in case of possible queries. The data collected will only be stored by us for as long as is necessary to process your enquiry and to contact you. They are then deleted.
Supplementary data protection information, in particular regarding your rights to information, correction, deletion, restriction of processing, objection and complaint, can be found in our data protection declaration.