Product development: Threaded plugs
Customised small series from the 3D printer
Special requirements and a low quantity were the challenge when it came an enquiry for threaded plugs. Thanks to 3D printing, a short term and cost-effective manufacturing of the small series was possible.
Initial situation: Solution needed for threaded plugs
Following a series of different post-processing steps on a high-pressure connection, a customer approached Würth Industrie Service with a request of manufacturing special threaded plugs (M38x1.5). The task was to prevent impurities in the interior of the high-pressure connection and the attached high pressure pump. The required quantity was 30 pieces.
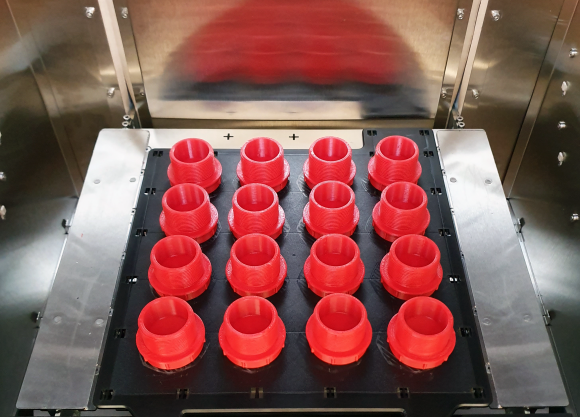
Additive manufacturing fulfils quality and economic requirements.
As the interplay between the fine threads and the specified thread length posed a challenge and the requested quantity was low, the possibilities of additive manufacturing came into the focus for the experts at Würth Industrie Service.
In the course of the collaborative project, the customer’s wishes were individually implemented when designing the threaded plug. The threaded plug was optimised consistently over the prepared CAD-model and the technical drawing after consultations with the customer until it matched their expectations.
The required quantity could subsequently be additively manufactured, packaged and sent to the customer within a day.
Series production with injection moulding
Since the demand for the individual stopper from the customer increased enormously, the stopper is now produced as a series using the injection moulding process. Due to the larger quantity requested, the conventional process is the more economical alternative. Würth Industrie Service continues to take care of the production and logistical provision.
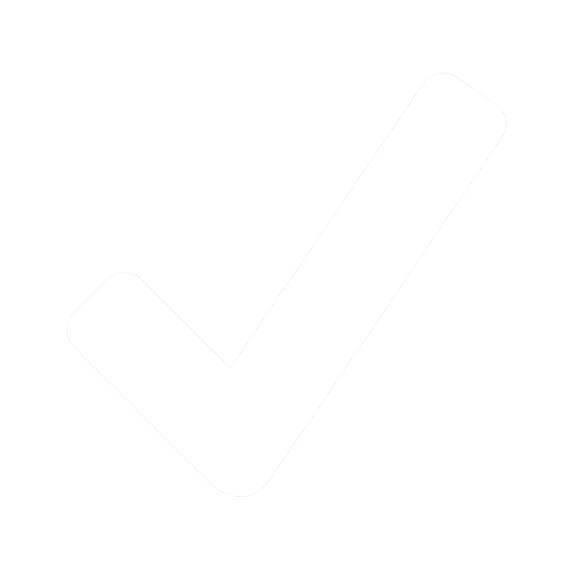
Factors of success
In the above mentioned example, additive manufacturing has significant advantages given the customisation and low production quantities over conventional procedures like injection moulding or subtractive procedures. The tool costs alone for injection moulding would have exceeded the value of the required quantity in comparison to additive manufacturing. Besides, the production and delivery times would have been significantly higher.
Through the continuous profitability check of Würth Industrie Service, the injection moulding process proved to be the more cost-effective option after a certain quantity of enquiries had been reached.
Additional information
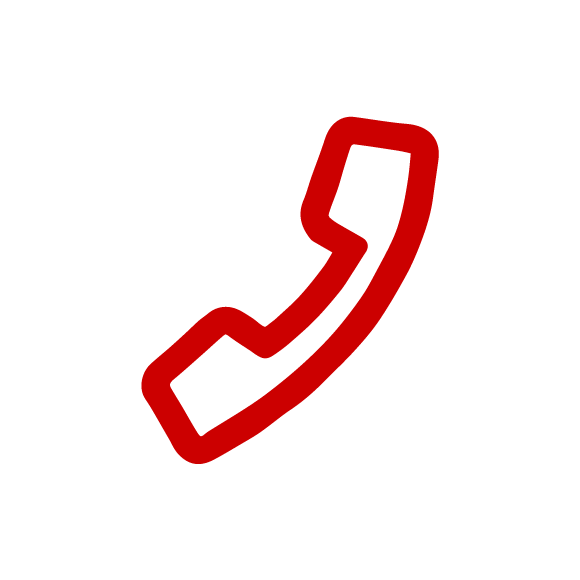
Contact
We are here for you!
Please contact us by telephone +49 7931 91-3288 or
via E-Mail under additivemanufacturing@wuerth-industrie.com.
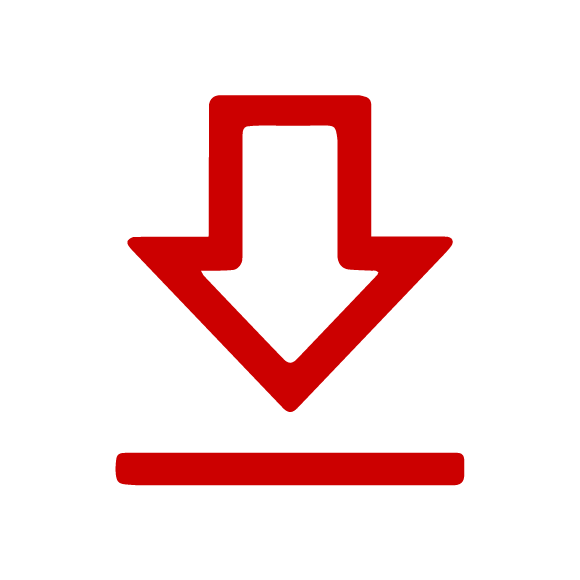
Websites can save or retrieve information in your browser in the form of Cookies. This may be anonymous statistical data, information about you, your settings or devices used, in order to enable a personalised web experience or so that the website works in the way you are expecting it to.
We respect your right to protection of your data. You can therefore decide not to accept certain types of Cookies. For an overview and the settings for the Cookies which we use, please see here. You can change these settings at any time, by invoking our Data protection declaration.
By saving, you confirm that you have understood the settings specified for Cookies and that you agree with them.
The Würth Industrie Service GmbH & Co. KG collects and processes the personal data provided in the form in order to process the requested request for you. Please note the mandatory fields in the forms. The legal basis for this processing, the absolutely necessary data, is Art. 6 para. 1 lit. b DSGVO, implementation of a pre-contractual measure. The processing of data voluntarily provided by you is carried out on the basis of Art. 6 para. 1 lit. f DSGVO. Thereafter, processing is permissible which is necessary to safeguard our legitimate interests. Our legitimate interest is to have contact with you, our customers, to improve our consulting quality and to be able to contact you more easily in case of possible queries. The data collected will only be stored by us for as long as is necessary to process your enquiry and to contact you. They are then deleted.
Supplementary data protection information, in particular regarding your rights to information, correction, deletion, restriction of processing, objection and complaint, can be found in our data protection declaration.